4
0
0
A Completely Continuous Tyre Pyrolysis Plant Could Work for a long time Without Interruption
100
Beston Machinery
0
Transport equipment, cars, trucks or others need rubber tyres for his or her smooth movement and those tend to get broken down after long use. The waste tyres were in earlier days put in landfills where they took a long time to decompose and led to environmental problems. It really is now easy to use continuous tyre pyrolysis plant to transform the waste tyres into oil, carbon black, and hydrocarbon gas, all byproducts who have a use. This may reduce waste in landfills and save the surroundings.
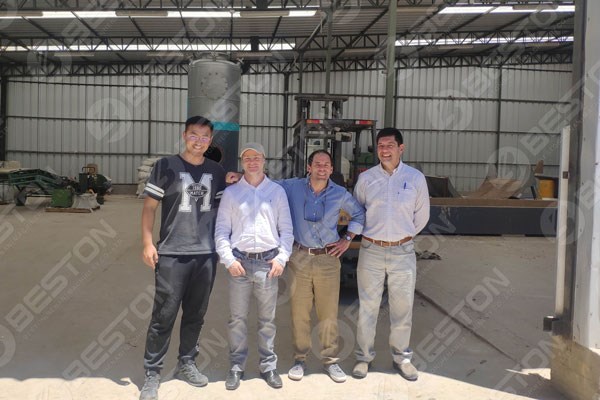
The entire process of Pyrolysis
The whole process of pyrolysis chemically decomposes the organic materials inside the tyre, mainly rubber, at quite high temperatures and does so in the lack of oxygen and under pressure. These could be up to 430°C (800°F). This changes the physical plus the chemical composition in the waste tyres and can be a procedure that cannot be reversed. Pyrolysis converts organic material in to a residue which contains ash, carbon and smaller quantities of oil and gas.
The Makeup of any Pyrolysis Plant
The main element of a pyrolysis plant is its reactor in which the waste tyres are heated using fuel, like wood, gas, or coal, and others. In this particular heating, oil gas is first produced and is also required to be brought to a condenser that can liquefy the gas straight into oil that needs to go to a oil tank. The gas that may be not condensed is led into the reactor to act as fuel for burning. After the reactor cools down carbon black is produced and should be removed. Steel, often utilized in radial tires can also be area of the residue after burning.
A pyrolysis plants can be designed being a fully continuous tyre pyrolysis plant that creates the byproducts without any need for cooling the reactor.
Continuous Tyre Pyrolysis Plants
A completely continuous tyre pyrolysis plant design allows all operations from the loading of the tyres to producing the various byproducts to be conducted without the interruption. Such plants will work all around the clock and all year round, provided that there exists a continuous flow of raw material - waste tyres. It really works just like an assembly line that constantly takes from the raw product and creates a constant flow of oil, carbon black and steel.
For continuous feeding waste tyres should be shredded and made in a smaller size. The tyres are fed in a shredding machine and cut to some size of a couple of". The shredding process also separates out the steel within the tyres and this could be retrieved magnetically from the shredders. The shredded material is automatically conveyed on the reactor, where heat is being generated. The oil gas finds it way to connected condensers where it really is converted into liquid oil that is then kept in tanks. Carbon black is produced at certain temperatures and automatically retrieved. Multiple reactors are used with the internal rotating system and heated with heat that utilizes other fuel or the oil gas for heating.
These plants that actually work continuously are controlled by computers and may be programmed, for all operations from feeding, burning and byproduct retrieval of carbon black, fuel oi and steel.
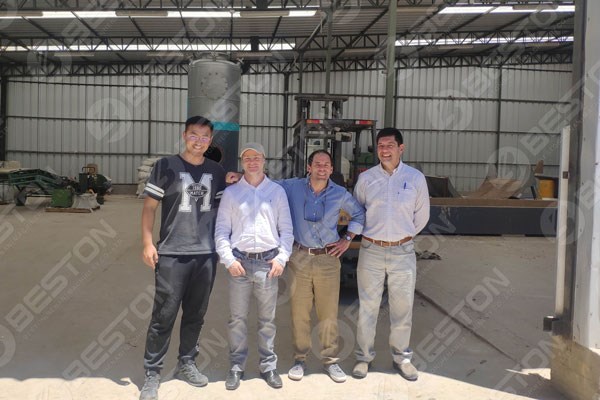
The entire process of Pyrolysis
The whole process of pyrolysis chemically decomposes the organic materials inside the tyre, mainly rubber, at quite high temperatures and does so in the lack of oxygen and under pressure. These could be up to 430°C (800°F). This changes the physical plus the chemical composition in the waste tyres and can be a procedure that cannot be reversed. Pyrolysis converts organic material in to a residue which contains ash, carbon and smaller quantities of oil and gas.
The Makeup of any Pyrolysis Plant
The main element of a pyrolysis plant is its reactor in which the waste tyres are heated using fuel, like wood, gas, or coal, and others. In this particular heating, oil gas is first produced and is also required to be brought to a condenser that can liquefy the gas straight into oil that needs to go to a oil tank. The gas that may be not condensed is led into the reactor to act as fuel for burning. After the reactor cools down carbon black is produced and should be removed. Steel, often utilized in radial tires can also be area of the residue after burning.
A pyrolysis plants can be designed being a fully continuous tyre pyrolysis plant that creates the byproducts without any need for cooling the reactor.
Continuous Tyre Pyrolysis Plants
A completely continuous tyre pyrolysis plant design allows all operations from the loading of the tyres to producing the various byproducts to be conducted without the interruption. Such plants will work all around the clock and all year round, provided that there exists a continuous flow of raw material - waste tyres. It really works just like an assembly line that constantly takes from the raw product and creates a constant flow of oil, carbon black and steel.
For continuous feeding waste tyres should be shredded and made in a smaller size. The tyres are fed in a shredding machine and cut to some size of a couple of". The shredding process also separates out the steel within the tyres and this could be retrieved magnetically from the shredders. The shredded material is automatically conveyed on the reactor, where heat is being generated. The oil gas finds it way to connected condensers where it really is converted into liquid oil that is then kept in tanks. Carbon black is produced at certain temperatures and automatically retrieved. Multiple reactors are used with the internal rotating system and heated with heat that utilizes other fuel or the oil gas for heating.
These plants that actually work continuously are controlled by computers and may be programmed, for all operations from feeding, burning and byproduct retrieval of carbon black, fuel oi and steel.
Signatur