16
0
0
How Exactly Does a Tire Pyrolysis Plant Work?
100
Beston Machinery
0
With the coming of pyrolysis plants, it’s now easy to make fuel oil using outdated tires. The pyrolysis plant will first process the tires in its reactor, accompanied by converting them into oil which can be used as fuel in cars and also the steel wire industry.
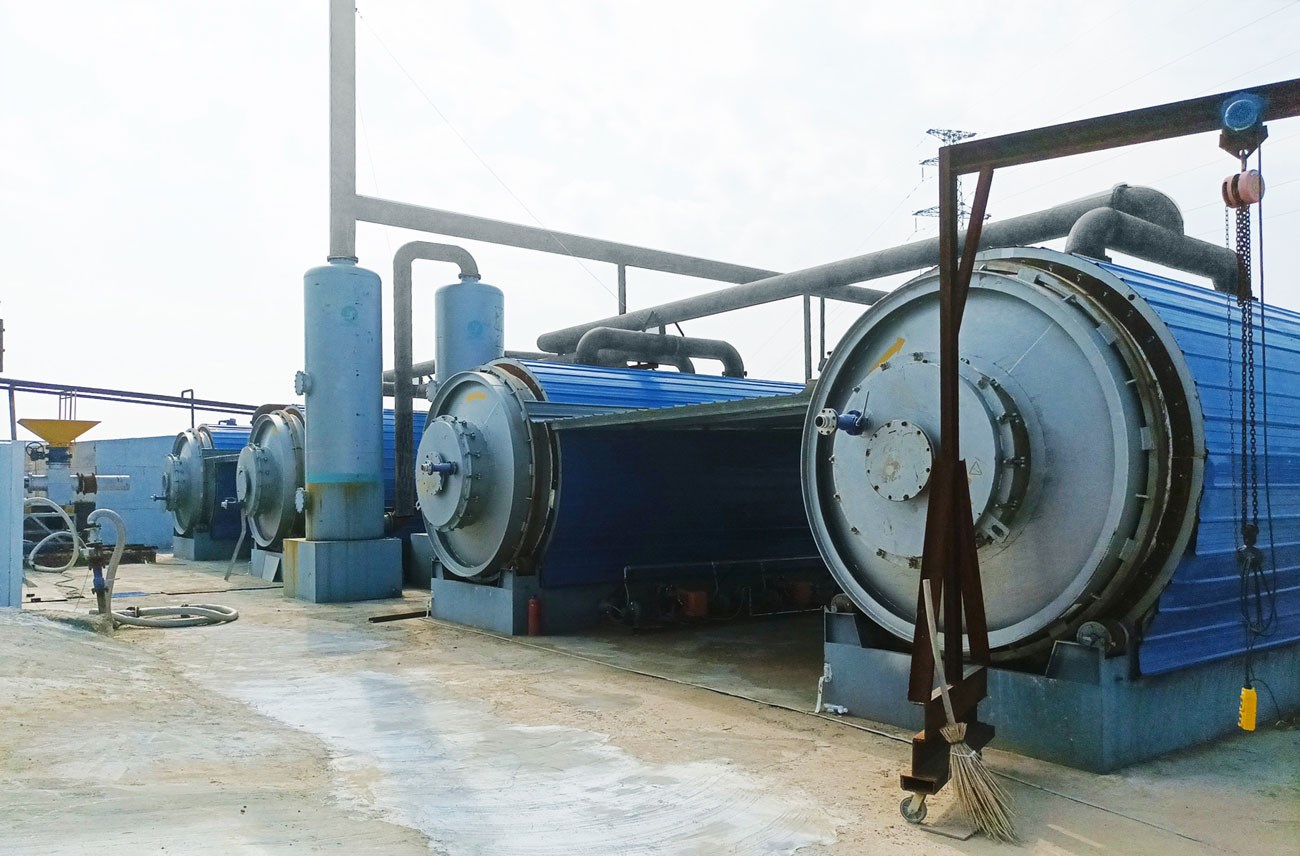
Working principle of any waste tyre pyrolysis machine
The working principle of a waste tyre pyrolysis machine necessitates the reactor heating waste tire and rubber and converting them into oil gas. In the next step, a condenser coverts the oil gas to generate liquid oil. This can be used liquid oil in different industries and also in your car or truck as fuel. A benefit on this oil is that it won’t react with the condenser while recycling, thus making sure the plant can get the most from its recyclable energy.
So how exactly does the plant work?
As well as worn-out tires and rubber, you may also use waste plastic as raw materials. The plant would melt the ingredients before processing them into fuel. Here’s just how the plant works:
1.Step one involves feeding the raw materials in the reactor. Most plants contain an automated feeding machine. You should pour the raw materials into this feeding machine and let it send them into the reactor slowly. Make sure there is enough space within the reactor for your materials to change and twist properly. It’s preferable to keep approximately one-third of the reactor empty to allow it to grind everything.
2.From the next step, the plant will heat the reactor so that it burns the waste tires and plastic. This could eventually produce combustible fuel. Right after the chamber within the reactor reaches 100o C, it starts releasing oil gas. Ever since the oil gas is heavy, it could separate itself slowly and get to the condenser in the next chamber.
The condenser is an additional crucial part of the plant that liquefies the oil gas and ensures that it drops in to a tank underneath. On the other hand, the lighter gas slowly rises to the very top of the condenser and liquefies later. This simply means the plant doesn’t leave any residue after you feed all of the raw materials. If you find any non-condensable gas left, it reaches the desulfurization system the location where the furnace connects together with the plant and sends the gas for recycling.
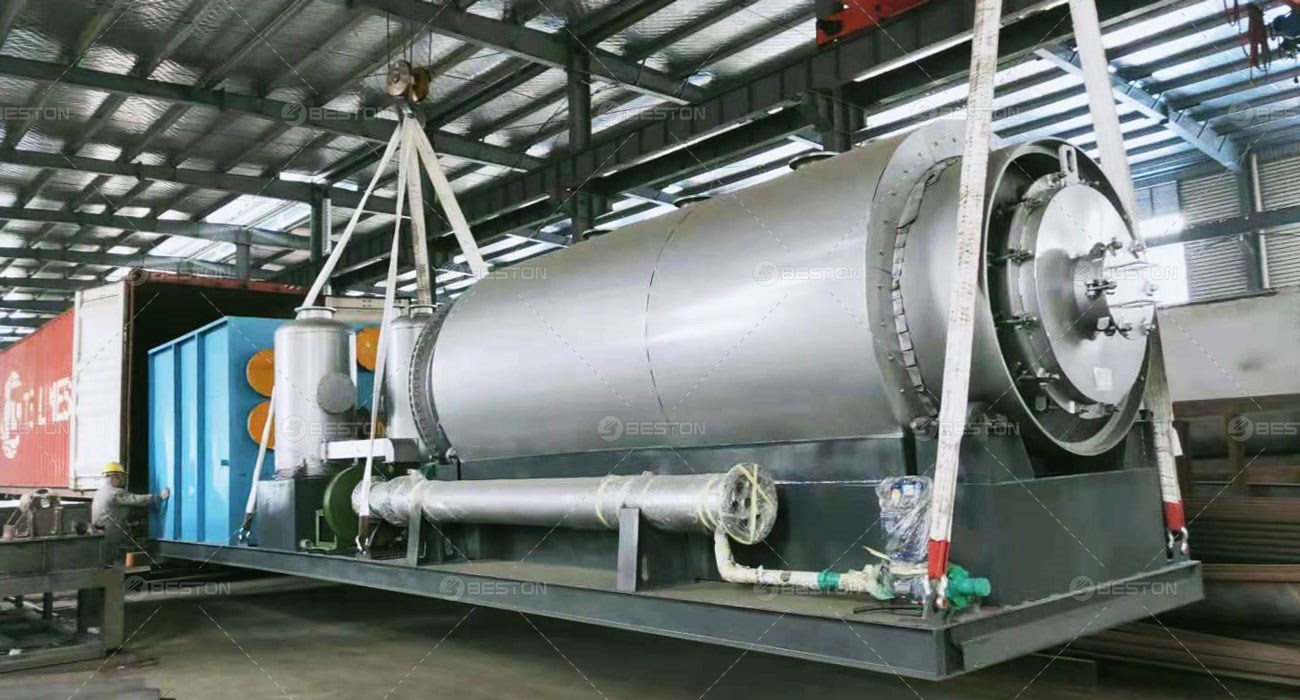
3.When the oil tank underneath the condenser collects the oil, it has to cool down so that it offers the fuel oil you want. The temperature must come down to a minimum of 40o C. And also this allows the carbon black to automatically discharge in the reactor.
4.The final step involves purifying the non-condensable gas. It has to experience several purification stages inside the smoke cleaning system in order that it later produces fuel oil. You will notice that it attains the emission standard set through the government. See this mobile pyrolysis unit.
One reason why a tire pyrolysis plant is indeed popular is that it leaves almost zero waste after every cycle. Above all, it recycles waste tires that individuals would certainly burn, which will, subsequently, bring about air pollution.
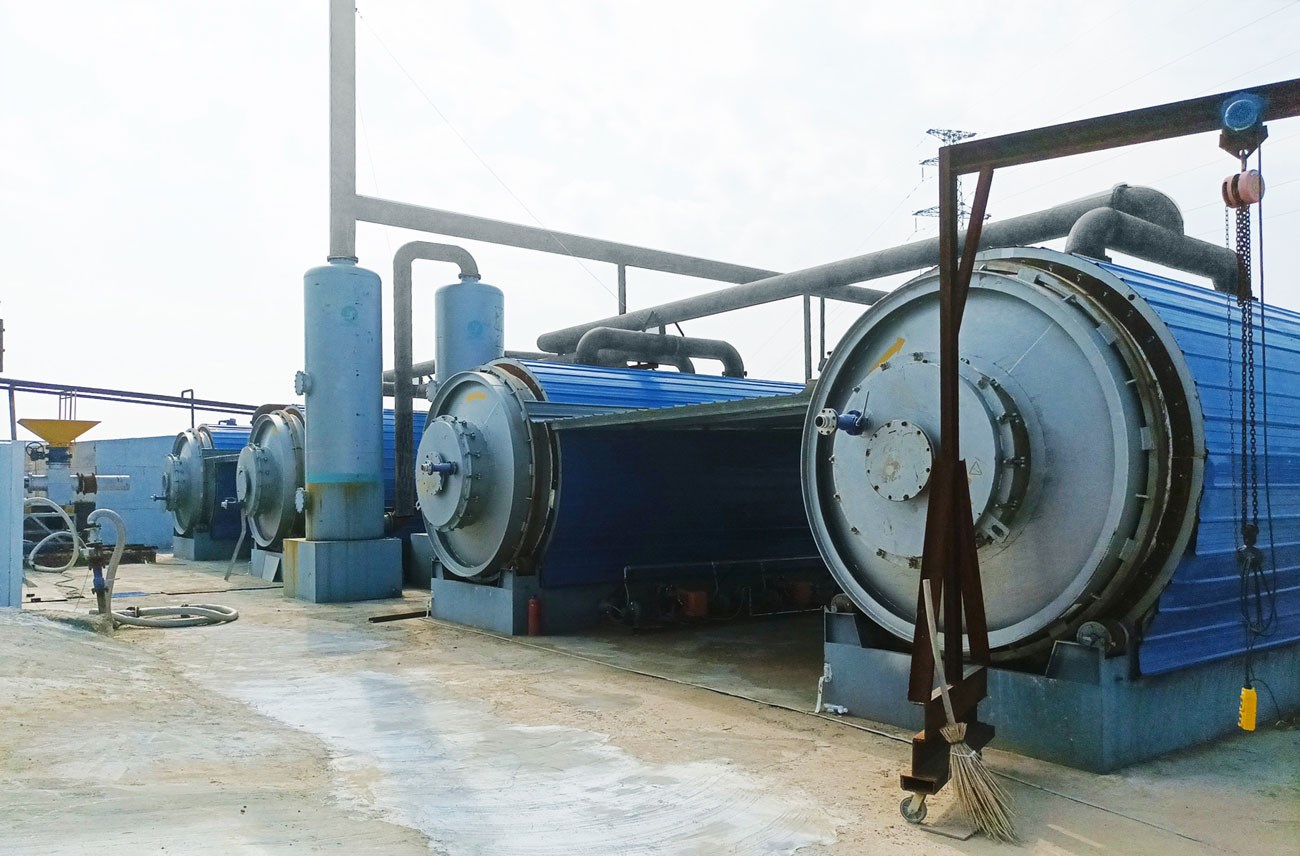
Working principle of any waste tyre pyrolysis machine
The working principle of a waste tyre pyrolysis machine necessitates the reactor heating waste tire and rubber and converting them into oil gas. In the next step, a condenser coverts the oil gas to generate liquid oil. This can be used liquid oil in different industries and also in your car or truck as fuel. A benefit on this oil is that it won’t react with the condenser while recycling, thus making sure the plant can get the most from its recyclable energy.
So how exactly does the plant work?
As well as worn-out tires and rubber, you may also use waste plastic as raw materials. The plant would melt the ingredients before processing them into fuel. Here’s just how the plant works:
1.Step one involves feeding the raw materials in the reactor. Most plants contain an automated feeding machine. You should pour the raw materials into this feeding machine and let it send them into the reactor slowly. Make sure there is enough space within the reactor for your materials to change and twist properly. It’s preferable to keep approximately one-third of the reactor empty to allow it to grind everything.
2.From the next step, the plant will heat the reactor so that it burns the waste tires and plastic. This could eventually produce combustible fuel. Right after the chamber within the reactor reaches 100o C, it starts releasing oil gas. Ever since the oil gas is heavy, it could separate itself slowly and get to the condenser in the next chamber.
The condenser is an additional crucial part of the plant that liquefies the oil gas and ensures that it drops in to a tank underneath. On the other hand, the lighter gas slowly rises to the very top of the condenser and liquefies later. This simply means the plant doesn’t leave any residue after you feed all of the raw materials. If you find any non-condensable gas left, it reaches the desulfurization system the location where the furnace connects together with the plant and sends the gas for recycling.
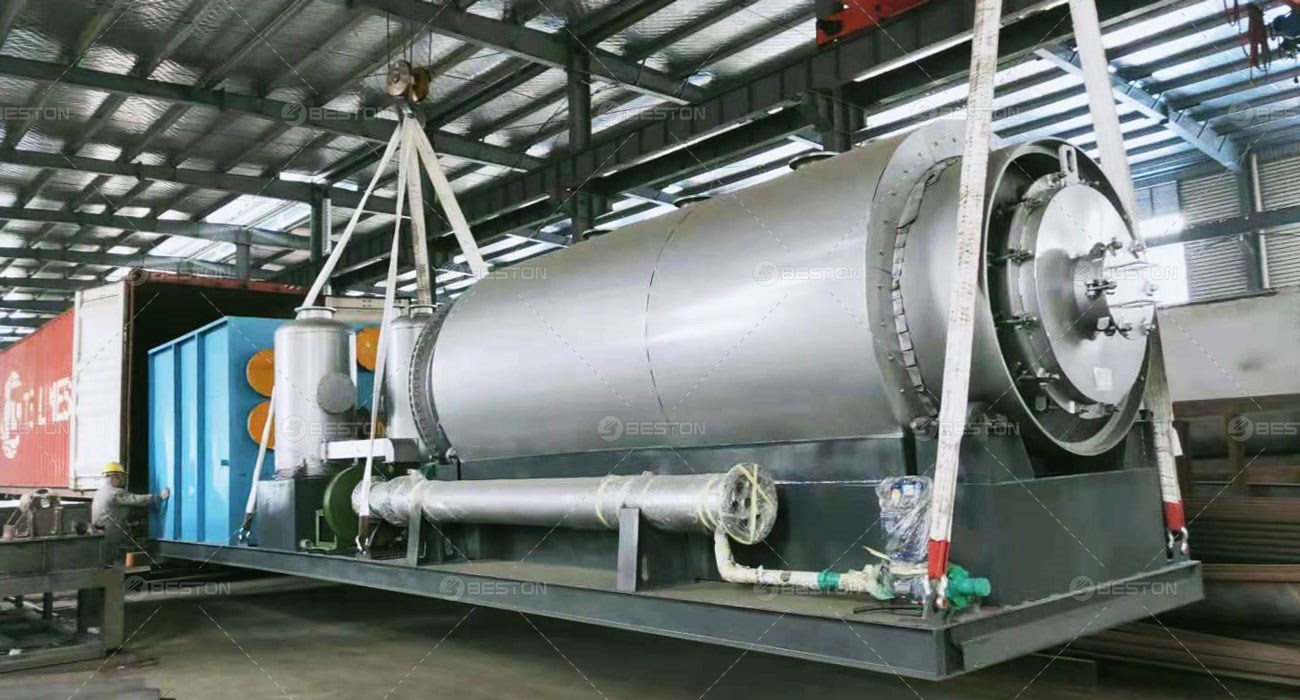
3.When the oil tank underneath the condenser collects the oil, it has to cool down so that it offers the fuel oil you want. The temperature must come down to a minimum of 40o C. And also this allows the carbon black to automatically discharge in the reactor.
4.The final step involves purifying the non-condensable gas. It has to experience several purification stages inside the smoke cleaning system in order that it later produces fuel oil. You will notice that it attains the emission standard set through the government. See this mobile pyrolysis unit.
One reason why a tire pyrolysis plant is indeed popular is that it leaves almost zero waste after every cycle. Above all, it recycles waste tires that individuals would certainly burn, which will, subsequently, bring about air pollution.
Signatur