6
0
0
The Working Mechanism of your Charcoal Manufacturing Machine
100
Beston Machinery
0
The most recent charcoal making machines include carbonization technology that converts biomass waste matter, municipal solid waste, and sewage sludge into charcoal. This sort of charcoal can successfully replace coal employed in power generation, thus lowering the world’s carbon footprint significantly.
Most modern Beston charcoal manufacturing plant works towards the principle of high-temperature pyrolysis. This technique forces the raw materials to generate various reactions within the carbonizing furnace. The reactions cause producing new energy that later makes chunks of charcoal. Some of the machines with advanced technology find their way into coconut shell charcoal making plants and rice husk charcoal making plants.
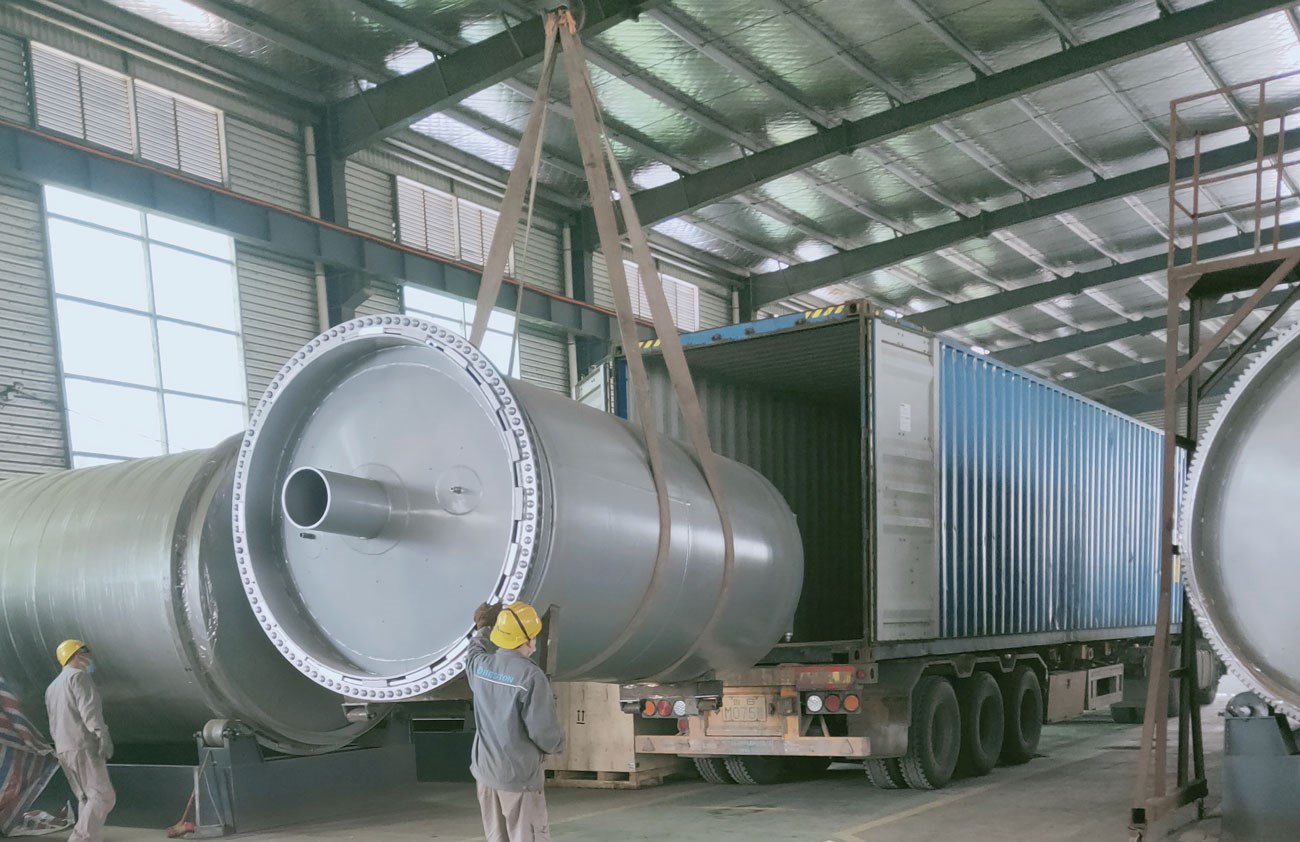
Modern charcoal making machines will be more eco-friendly compared to the traditional carbonization process. They achieve higher efficiency, high quality, and better output than their traditional counterparts.
Charcoal carbonization process
Making carbon from waste materials is not any joke. Here’s the comprehensive method that will amaze you how modern technology might help in lessening the world’s overall carbon footprint:
1. A number of the raw materials used in a charcoal manufacturing machine are biomass waste, coconut shell, wood, straw, rice husk, sawdust, palm shell, and peanut shell.
2. The carbonization equipment makes it necessary that the raw materials’ moisture ought to be below 20%. However, the actual size of the raw materials needs to be at the very least 30 mm. Otherwise, the device can’t process the raw materials properly. Usually, carbon manufacturers get a pretreatment device that segregates different types of raw materials, making it simpler for your carbonization equipment to combine the materials easily.
3. The raw materials enter the carbonization furnace after preprocessing. Next, the machine relies on a few traditional fuels, such as gas, wood, or coal to heat the furnace for a minimum of 30 minutes. The carbonization furnace starts generating combustible gas once the furnace reaches its desired temperature. Usually, it requires 15 to 20 mins for the furnace to process the raw materials with a temperature between 650 and 780o C.
4. Discharging the coal just after processing is dangerous. Manufacturers make use of a air conditioning to significantly decrease the charcoal’s temperature to 30o C. Hot charcoal could cause life-threatening accidents when it comes in contact with oxygen. That’s why charcoal making machines come with a air conditioning in order to avoid perils associated with fire within the plant. A few of the advanced machines have got a full-sealed chamber, thus making this process safer. View the this page right now https://bestonmachinery.com/biochar-production-equipment/mobile/.
5. The combustible gas within the carbonization process undergoes a purification stage where a spray dusting system removes sulfur components as a result. These sulfur components later go into the heat furnace to produce charcoal. Therefore, there is not any waste left through the waste matter that you simply put into the carbonization chamber in the first step.
6. Apart from the sulfur components, the condenser system also liquefies combustible gas into wood vinegar and tar.
Because of so many benefits, it is possible to realize why you will discover a worldwide requirement for a charcoal manufacturing machine. It offers the potential to lessen pollution and make the globe a greener place for everyone.
Most modern Beston charcoal manufacturing plant works towards the principle of high-temperature pyrolysis. This technique forces the raw materials to generate various reactions within the carbonizing furnace. The reactions cause producing new energy that later makes chunks of charcoal. Some of the machines with advanced technology find their way into coconut shell charcoal making plants and rice husk charcoal making plants.
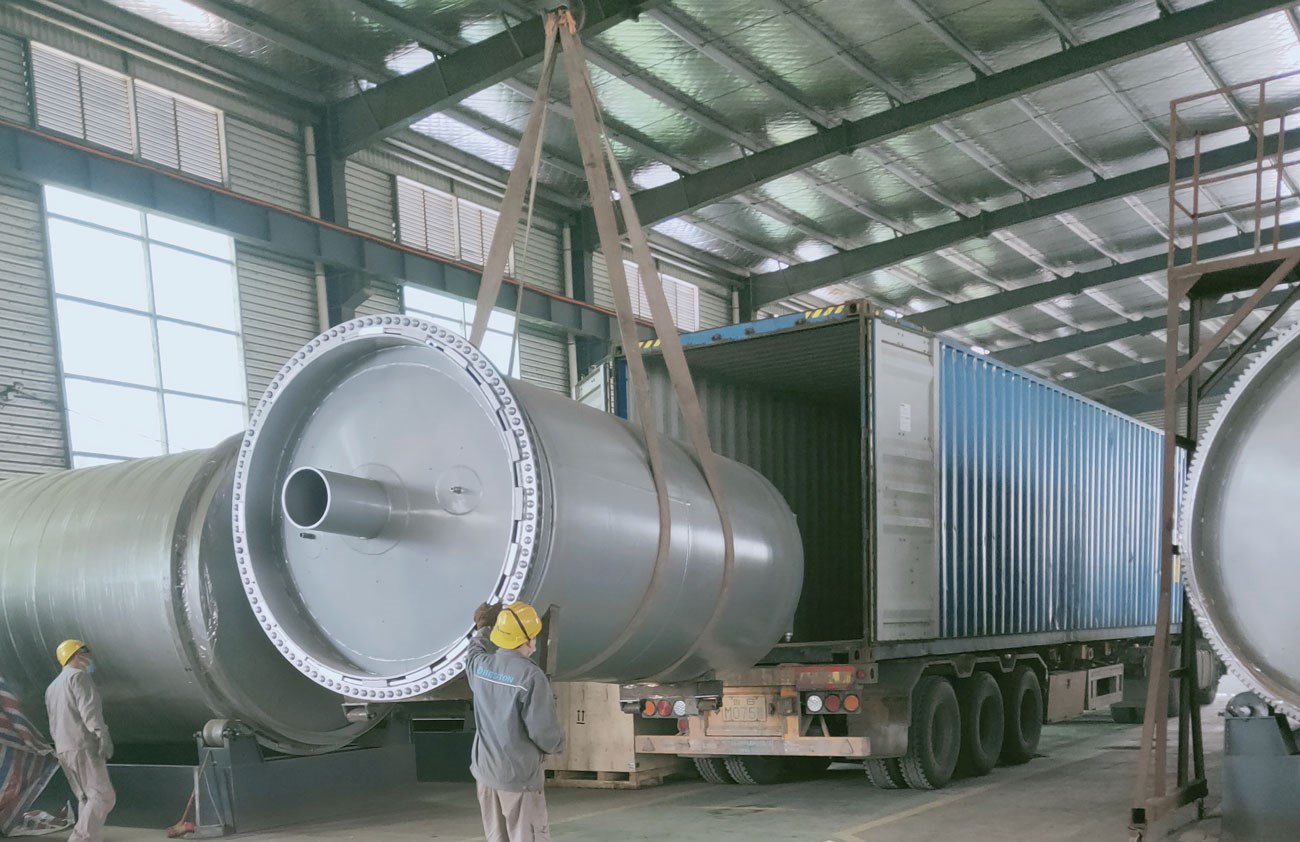
Modern charcoal making machines will be more eco-friendly compared to the traditional carbonization process. They achieve higher efficiency, high quality, and better output than their traditional counterparts.
Charcoal carbonization process
Making carbon from waste materials is not any joke. Here’s the comprehensive method that will amaze you how modern technology might help in lessening the world’s overall carbon footprint:
1. A number of the raw materials used in a charcoal manufacturing machine are biomass waste, coconut shell, wood, straw, rice husk, sawdust, palm shell, and peanut shell.
2. The carbonization equipment makes it necessary that the raw materials’ moisture ought to be below 20%. However, the actual size of the raw materials needs to be at the very least 30 mm. Otherwise, the device can’t process the raw materials properly. Usually, carbon manufacturers get a pretreatment device that segregates different types of raw materials, making it simpler for your carbonization equipment to combine the materials easily.
3. The raw materials enter the carbonization furnace after preprocessing. Next, the machine relies on a few traditional fuels, such as gas, wood, or coal to heat the furnace for a minimum of 30 minutes. The carbonization furnace starts generating combustible gas once the furnace reaches its desired temperature. Usually, it requires 15 to 20 mins for the furnace to process the raw materials with a temperature between 650 and 780o C.
4. Discharging the coal just after processing is dangerous. Manufacturers make use of a air conditioning to significantly decrease the charcoal’s temperature to 30o C. Hot charcoal could cause life-threatening accidents when it comes in contact with oxygen. That’s why charcoal making machines come with a air conditioning in order to avoid perils associated with fire within the plant. A few of the advanced machines have got a full-sealed chamber, thus making this process safer. View the this page right now https://bestonmachinery.com/biochar-production-equipment/mobile/.
5. The combustible gas within the carbonization process undergoes a purification stage where a spray dusting system removes sulfur components as a result. These sulfur components later go into the heat furnace to produce charcoal. Therefore, there is not any waste left through the waste matter that you simply put into the carbonization chamber in the first step.
6. Apart from the sulfur components, the condenser system also liquefies combustible gas into wood vinegar and tar.
Because of so many benefits, it is possible to realize why you will discover a worldwide requirement for a charcoal manufacturing machine. It offers the potential to lessen pollution and make the globe a greener place for everyone.
Signatur