20
0
0
Production Process Of Waste Plastic Pyrolysis Plant
41
NO.99 South University Road, Zhengzhou City, Henan Province, China
0
Plastic waste pollution has become a pressing issue in our modern world. The accumulation of plastic waste in landfills and oceans poses significant environmental challenges. To combat this problem, waste plastic pyrolysis plants have emerged as a promising solution. These plants utilize advanced technology to convert waste plastic into valuable products through the process of pyrolysis. In this article, we will delve into the intricate production process of waste plastic pyrolysis plants, shedding light on their importance in addressing plastic waste pollution.
Understanding Waste Plastic Pyrolysis Plants
Before we explore the production process, it is essential to grasp the concept of waste plastic pyrolysis plants. These innovative plants are designed specifically to transform various types of waste plastic into useful end products, such as liquid fuel and carbon black, through the process of pyrolysis. A typical waste plastic pyrolysis plant comprises several key components, each playing a vital role in the overall efficiency and effectiveness of the process.
Components of a typical waste plastic pyrolysis plant include a feeding system, a pyrolysis reactor, a cooling system, a condensing system, a gas cleaning system, and a discharging system. The feeding system ensures a continuous supply of waste plastic to the plant. The pyrolysis reactor is the heart of the plant, where the actual pyrolysis process takes place. The cooling system facilitates the efficient cooling of the pyrolysis products, allowing the collection of liquid and solid end products. The condensing system condenses the volatile gases produced during pyrolysis into liquid fuel. The gas cleaning system ensures the removal of impurities and pollutants from the pyrolysis gas, while the discharging system collects and stores the final products for further utilization or disposal.
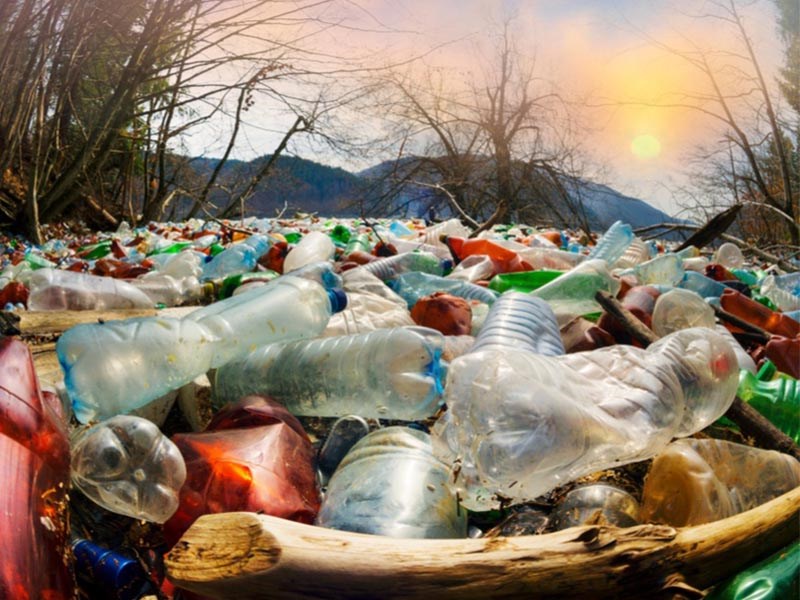
Step-by-Step Production Process of Waste Plastic Pyrolysis Plant
To better understand how a waste plastic pyrolysis plant operates, let's delve into the step-by-step production process involved:
Stage 1: Feeding the plant with waste plastic
The initial stage of the production process involves feeding the plant with various types of waste plastic. Different types of plastic, such as polyethylene, polypropylene, and polystyrene, are suitable for pyrolysis. However, it is important to properly sort and prepare the waste plastic to ensure optimal results. Sorting helps separate different types of plastic, while preparation involves removing any non-plastic contaminants, such as paper or metal.
Stage 2: Pyrolysis process
Once the waste plastic is fed into the pyrolysis reactor, the pyrolysis process begins. Pyrolysis is a thermochemical decomposition process that occurs in the absence of oxygen. In this stage, the waste plastic is heated to high temperatures, typically ranging from 300 to 500 degrees Celsius. As the temperature rises, the long polymer chains in the plastic break down into smaller molecules, resulting in the formation of liquid fuel, gases, and solid residue.
Stage 3: Cooling and condensing
After the pyrolysis process, the resulting products are extremely hot and require rapid cooling. The cooling system within the plant facilitates this process, allowing the collection of liquid and solid end products. Efficient cooling ensures the condensation of the volatile gases into liquid fuel, which can be further processed or utilized. The solid residue, known as carbon black, is also collected for potential applications.
Stage 4: Gas cleaning and filtration
The pyrolysis gases produced during the process contain impurities and pollutants that need to be removed. The gas cleaning system within the waste plastic pyrolysis plant plays a crucial role in filtering out these impurities, ensuring cleaner emissions. Filtration systems, such as cyclones and scrubbers, help in the removal of particulate matter and harmful gases, resulting in a cleaner and safer operation.
Stage 5: Discharging and collection of end products
Once the production process is complete, the final products, including liquid fuel and carbon black, are discharged and collected. Proper storage and handling of these end products are essential to maintain their quality and facilitate further utilization or disposal. The liquid fuel can be used as a source of energy or refined for specific applications, while carbon black finds uses in various industries, including rubber manufacturing and ink production.
Advantages of Waste Plastic Pyrolysis Plants
Waste plastic pyrolysis plants offer numerous advantages in addressing plastic waste pollution and promoting sustainability:
Recycling and reducing plastic waste pollution: By converting waste plastic into valuable products, these plants contribute to reducing the amount of plastic waste ending up in landfills or polluting our environment. It provides a viable recycling solution for non-recyclable plastics.
Production of valuable end products: The pyrolysis process yields valuable end products, such as liquid fuel and carbon black. The liquid fuel can serve as an alternative source of energy, reducing dependence on fossil fuels. Carbon black, on the other hand, has various industrial applications, contributing to resource recovery.
Energy generation and resource recovery: The liquid fuel produced through pyrolysis can be used as a substitute for conventional fuels in industrial processes or power generation. This helps conserve natural resources and reduce greenhouse gas emissions associated with traditional fuel consumption.
Environmental benefits and carbon footprint reduction: Waste plastic pyrolysis plants contribute to mitigating environmental pollution by minimizing plastic waste accumulation and reducing the carbon footprint associated with plastic production and disposal. It promotes a circular economy approach to plastic waste management.
Challenges and Considerations in Waste Plastic Pyrolysis
While waste plastic pyrolysis plants offer significant benefits, several challenges and considerations should be taken into account:
Quality and composition of the waste plastic: The quality and composition of the waste plastic greatly influence the efficiency and yield of the pyrolysis process. Contaminants or incompatible plastics can affect the quality of the end products and require additional purification steps.
Energy consumption and process efficiency: The energy required to heat the pyrolysis reactor and sustain the process is an important consideration. Improving energy efficiency through advanced technologies and heat recovery systems can enhance the overall sustainability of waste plastic pyrolysis plants.
Safety measures and environmental regulations: The operation of waste plastic pyrolysis plants should adhere to strict safety guidelines and comply with environmental regulations. Proper handling of potentially hazardous substances, emission control, and waste management are crucial aspects to ensure a safe and sustainable operation.
Waste management and proper disposal of byproducts: The proper management and disposal of the byproducts, such as carbon black and non-condensable gases, should be taken into account. Developing efficient strategies for utilization or safe disposal of these byproducts is essential to maximize the environmental benefits of waste plastic pyrolysis.
Conclusion
The production process of waste plastic pyrolysis plants involves several stages, including feeding, pyrolysis, cooling and condensing, gas cleaning, and discharging of end products. These plants play a vital role in addressing plastic waste pollution by transforming waste plastic into valuable products. They contribute to recycling efforts, resource recovery, and the reduction of greenhouse gas emissions. However, challenges such as waste plastic quality, energy consumption, and adherence to safety and environmental regulations must be considered. Embracing waste plastic pyrolysis technology offers a promising solution to combat plastic waste pollution and foster a more sustainable future.
Understanding Waste Plastic Pyrolysis Plants
Before we explore the production process, it is essential to grasp the concept of waste plastic pyrolysis plants. These innovative plants are designed specifically to transform various types of waste plastic into useful end products, such as liquid fuel and carbon black, through the process of pyrolysis. A typical waste plastic pyrolysis plant comprises several key components, each playing a vital role in the overall efficiency and effectiveness of the process.
Components of a typical waste plastic pyrolysis plant include a feeding system, a pyrolysis reactor, a cooling system, a condensing system, a gas cleaning system, and a discharging system. The feeding system ensures a continuous supply of waste plastic to the plant. The pyrolysis reactor is the heart of the plant, where the actual pyrolysis process takes place. The cooling system facilitates the efficient cooling of the pyrolysis products, allowing the collection of liquid and solid end products. The condensing system condenses the volatile gases produced during pyrolysis into liquid fuel. The gas cleaning system ensures the removal of impurities and pollutants from the pyrolysis gas, while the discharging system collects and stores the final products for further utilization or disposal.
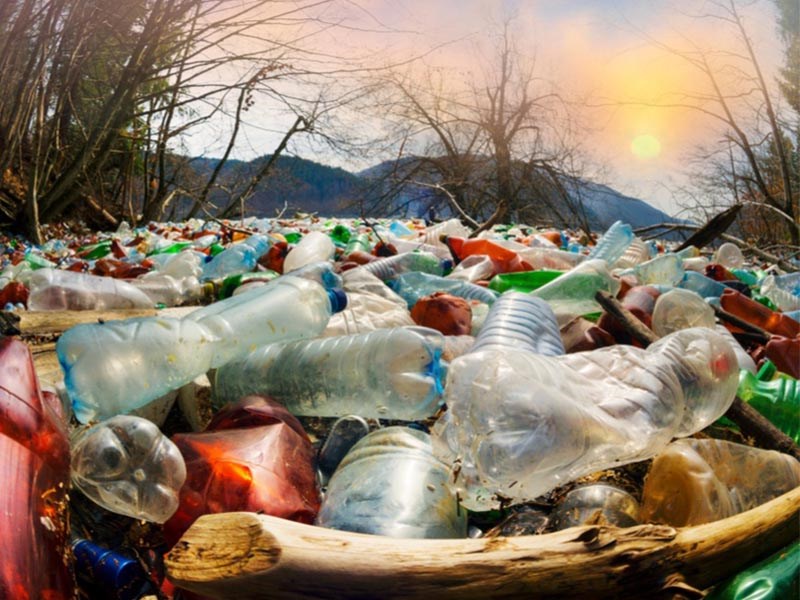
Step-by-Step Production Process of Waste Plastic Pyrolysis Plant
To better understand how a waste plastic pyrolysis plant operates, let's delve into the step-by-step production process involved:
Stage 1: Feeding the plant with waste plastic
The initial stage of the production process involves feeding the plant with various types of waste plastic. Different types of plastic, such as polyethylene, polypropylene, and polystyrene, are suitable for pyrolysis. However, it is important to properly sort and prepare the waste plastic to ensure optimal results. Sorting helps separate different types of plastic, while preparation involves removing any non-plastic contaminants, such as paper or metal.
Stage 2: Pyrolysis process
Once the waste plastic is fed into the pyrolysis reactor, the pyrolysis process begins. Pyrolysis is a thermochemical decomposition process that occurs in the absence of oxygen. In this stage, the waste plastic is heated to high temperatures, typically ranging from 300 to 500 degrees Celsius. As the temperature rises, the long polymer chains in the plastic break down into smaller molecules, resulting in the formation of liquid fuel, gases, and solid residue.
Stage 3: Cooling and condensing
After the pyrolysis process, the resulting products are extremely hot and require rapid cooling. The cooling system within the plant facilitates this process, allowing the collection of liquid and solid end products. Efficient cooling ensures the condensation of the volatile gases into liquid fuel, which can be further processed or utilized. The solid residue, known as carbon black, is also collected for potential applications.
Stage 4: Gas cleaning and filtration
The pyrolysis gases produced during the process contain impurities and pollutants that need to be removed. The gas cleaning system within the waste plastic pyrolysis plant plays a crucial role in filtering out these impurities, ensuring cleaner emissions. Filtration systems, such as cyclones and scrubbers, help in the removal of particulate matter and harmful gases, resulting in a cleaner and safer operation.
Stage 5: Discharging and collection of end products
Once the production process is complete, the final products, including liquid fuel and carbon black, are discharged and collected. Proper storage and handling of these end products are essential to maintain their quality and facilitate further utilization or disposal. The liquid fuel can be used as a source of energy or refined for specific applications, while carbon black finds uses in various industries, including rubber manufacturing and ink production.
Advantages of Waste Plastic Pyrolysis Plants
Waste plastic pyrolysis plants offer numerous advantages in addressing plastic waste pollution and promoting sustainability:
Recycling and reducing plastic waste pollution: By converting waste plastic into valuable products, these plants contribute to reducing the amount of plastic waste ending up in landfills or polluting our environment. It provides a viable recycling solution for non-recyclable plastics.
Production of valuable end products: The pyrolysis process yields valuable end products, such as liquid fuel and carbon black. The liquid fuel can serve as an alternative source of energy, reducing dependence on fossil fuels. Carbon black, on the other hand, has various industrial applications, contributing to resource recovery.
Energy generation and resource recovery: The liquid fuel produced through pyrolysis can be used as a substitute for conventional fuels in industrial processes or power generation. This helps conserve natural resources and reduce greenhouse gas emissions associated with traditional fuel consumption.
Environmental benefits and carbon footprint reduction: Waste plastic pyrolysis plants contribute to mitigating environmental pollution by minimizing plastic waste accumulation and reducing the carbon footprint associated with plastic production and disposal. It promotes a circular economy approach to plastic waste management.
Challenges and Considerations in Waste Plastic Pyrolysis
While waste plastic pyrolysis plants offer significant benefits, several challenges and considerations should be taken into account:
Quality and composition of the waste plastic: The quality and composition of the waste plastic greatly influence the efficiency and yield of the pyrolysis process. Contaminants or incompatible plastics can affect the quality of the end products and require additional purification steps.
Energy consumption and process efficiency: The energy required to heat the pyrolysis reactor and sustain the process is an important consideration. Improving energy efficiency through advanced technologies and heat recovery systems can enhance the overall sustainability of waste plastic pyrolysis plants.
Safety measures and environmental regulations: The operation of waste plastic pyrolysis plants should adhere to strict safety guidelines and comply with environmental regulations. Proper handling of potentially hazardous substances, emission control, and waste management are crucial aspects to ensure a safe and sustainable operation.
Waste management and proper disposal of byproducts: The proper management and disposal of the byproducts, such as carbon black and non-condensable gases, should be taken into account. Developing efficient strategies for utilization or safe disposal of these byproducts is essential to maximize the environmental benefits of waste plastic pyrolysis.
Conclusion
The production process of waste plastic pyrolysis plants involves several stages, including feeding, pyrolysis, cooling and condensing, gas cleaning, and discharging of end products. These plants play a vital role in addressing plastic waste pollution by transforming waste plastic into valuable products. They contribute to recycling efforts, resource recovery, and the reduction of greenhouse gas emissions. However, challenges such as waste plastic quality, energy consumption, and adherence to safety and environmental regulations must be considered. Embracing waste plastic pyrolysis technology offers a promising solution to combat plastic waste pollution and foster a more sustainable future.
Signatur